La última prueba del no solo fue una gran oportunidad para disfrutar de las 8H de Bahrein, sino también para contar sus historias más particulares entre bastidores. A la localidad de Sakhir, donde se encuentra el trazado, se llega tras una media hora en coche desde los rascacielos que caracterizan el centro de Manama, atravesando la autopista rodeada de palmeras y dunas de arena, hasta llegar a las dos curvas que conducen a la pista.
La avenida que discurre junto a ella, si se recorre hasta el final, conduce a la sede de Racing Force Group, lÃder mundial en equipamiento de seguridad para el automovilismo fundado en 2021, con sede principal en Ronco Scrivia [Génova], y que incluye las marcas OMP, Bell Racing, Zeronoise y Racing Spirit. El grupo cuenta ahora con siete sedes en todo el mundo, incluidas las de Bélgica y Estados Unidos, pero sigue siendo de capital italiano, y la planta de Oriente Medio para la producción de cascos Bell tomó forma en 2015 gracias a la financiación del gobierno local.
En las últimas semanas, concluyó la ampliación de las instalaciones de Sakhir, duplicando la superficie, de ahora 12.000 metros cuadrados, y la capacidad de producción, tanto de cascos de competición como de minicascos coleccionables a escala 1:2, mientras que Mumtalakat, el fondo soberano del paÃs, se convirtió desde 2024 en accionista del grupo, financiando también la construcción de una segunda planta de producción, que se levantará junto a la actual.
“Desde 2015, nuestra asociación con el BIC [Bahrain International Circuit] es cada vez más estrecha, lo que nos garantiza las mejores condiciones y recursos para confirmarnos como lÃderes en la producción de cascos de última generación para deportes de motor. La finalización de la ampliación de la sede de Sakhir es otro paso clave en esta alianza de gran éxito”, dijo el director del Racing Force Bahrain y Force Group, Stephane Cohen.
“Empezando por Bell Racing Helmets, el vÃnculo con el BIC se ha extendido a todo Racing Force Group, y tras la inversión en Mumtalakat podemos anunciar el inicio de la construcción de una segunda planta en Sakhir. Será una baza estratégica para aumentar la producción global de componentes de la gama OMP, otra referencia absoluta en el mundo de la competición”, continuó. “En nombre de todo el grupo, me gustarÃa dar las gracias una vez más a la organización del Circuito Internacional de Bahréin, al CEO Sheikh Salman bin Isa Al Khalifa, a Mumtalakat y a toda la comunidad local de Bahréin por su continuo apoyo.”
El director del trazado, el jeque Salman bin Isa Al Khalifa, añadió: “La finalización de la ampliación de la fábrica de Bell Racing Helmets y el inicio de las obras de las nuevas instalaciones de OMP son dos hitos más en la exitosa asociación con Racing Force Group. Estamos encantados de poder apoyar a marcas tan históricas y respetadas en el deporte del motor”.
“Nuestra asociación refleja la posición de BIC como sede del automovilismo en Oriente Medio en su sentido más amplio, y doy las gracias a todas las entidades de Bahrein que facilitan nuestros esfuerzos, especialmente a Mumtalakat”, explicó.
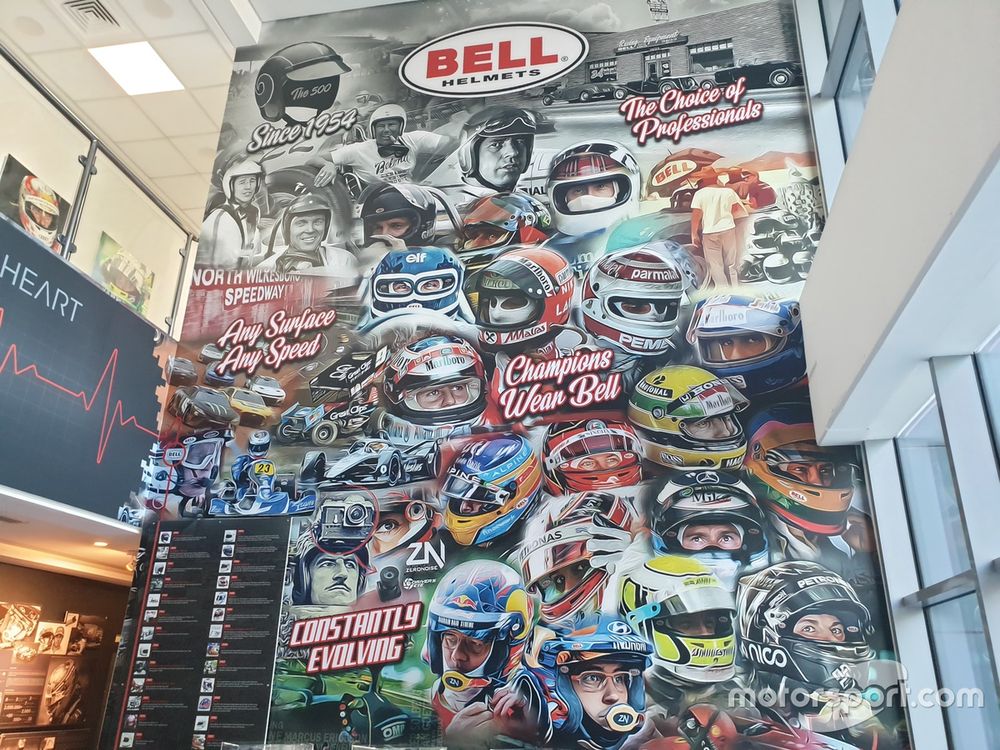
La historia de Bell y los cascos
Al entrar en el vestÃbulo principal, uno no puede evitar quedarse boquiabierto ante los dos murales que abrazan al visitante y al trabajador. A la izquierda hay pilotos con equipación OMP y enmarcados los monos de y Michael Schumacher, mientras que a la derecha hay cascos Bell con los rostros de los protagonistas de varias épocas del automovilismo, además de algunos ejemplos que empiezan a mostrar lo mucho que cambió la empresa con sus productos a lo largo del tiempo.
La producción comenzó en Estados Unidos en 1954, y tres años después llegó el modelo 500 TX con el primer tejido interno para la absorción de impactos, que con su evolución continua dio lugar al Star, el primer casco integral que llevó a la competición en 1968, convirtiéndose en el objeto de protección por excelencia en la década siguiente.
Aquà tenemos también el primer casco capaz de resistir las llamas, que desde 1973 hasta nuestros dÃas experimentó una enorme evolución, como te mostraremos más adelante, a través de la construcción con materiales compuestos como el Kevlar y la fibra de carbono. En el mundo de la competición, la ropa también va deprisa, y los cascos no son menos gracias a la continua experimentación y modificaciones entre la década de 1980 y 1990, hasta llegar al modelo HP77 de hoy en dÃa equipado con viseras reforzadas tras el accidente de Felipe Massa en el Gran Premio de HungrÃa 2009 mediante materiales a prueba de balas y diseños que adoptan funciones aerodinámicas y una mejor ventilación.
Al mismo tiempo, hay cascos para rallies con sistemas de comunicación integrados y, desde el año pasado, incluso una función inalámbrica que permite al piloto y al navegante continuar las conversaciones incluso fuera del coche, gracias a una unidad de control que actúa como repetidor y permite la conexión sin cables como ocurre dentro del cockpit.
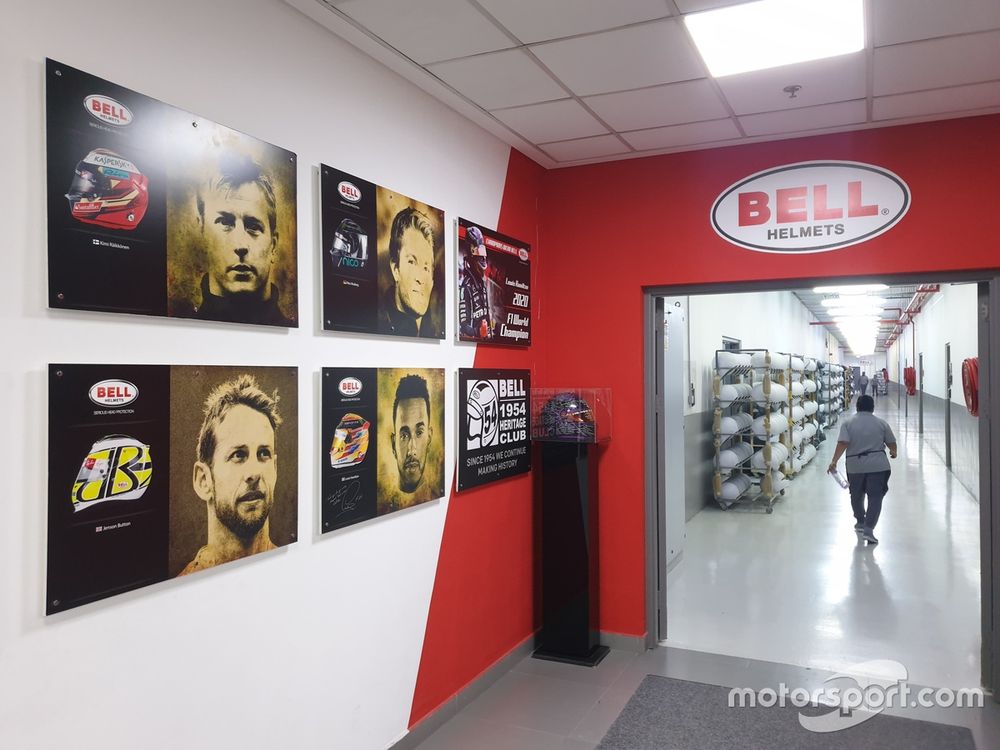
Las puertas abiertas de Bell
Es un auténtico viaje por capÃtulos que iniciamos con la apertura de las puertas de la fábrica a los distintos departamentos de elaboración, en una empresa en la que trabajan unos 400 empleados, recibidos por el Bell Hall of Fame por los rostros de los distintos pilotos que lucen los mencionados cascos, con mucho espacio para los autógrafos.
Ya en el pasillo, nos fijamos en los carros con los cascos en distintos estados de su preparación, pero yendo por orden, el lado izquierdo es el de los departamentos de preparación de los distintos componentes, mientras que a la derecha está el de la cadena de montaje. Empezamos con una especie de calota protectora interna que VARÃa sus medidas según las necesidades, una primera estratificación de un casco con las correspondientes pruebas de resistencia que hay que superar y una densidad interna que VARÃa según la competición para la que se vaya a usar el producto final.
Continuando, pasamos por las salas de investigación y desarrollo en las que se estudian pequeños añadidos, como apéndices aerodinámicos y otros accesorios de este tipo solicitados por equipos y pilotos, mientras que en las estanterÃas hay materiales de desecho que siempre se reutilizan para los minicascos, lo que confirma lo fiel que puede ser la reproducción.
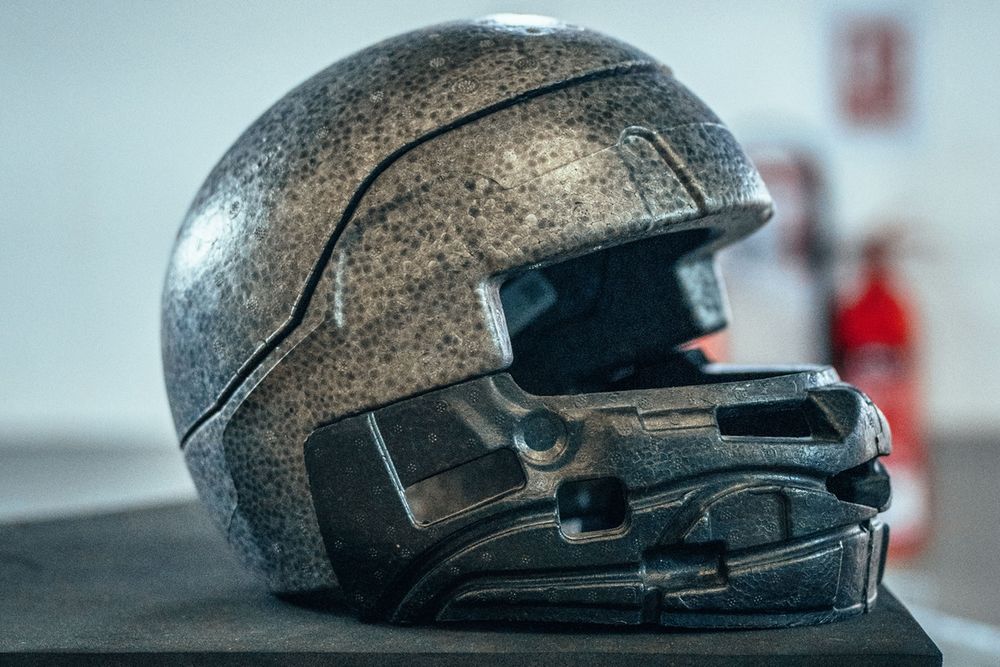
El casco toma forma en Bell
El siguiente departamento es donde se lamina la carcasa del casco, dándole su forma redondeada mediante la unión de la primera capa con fibra de vidrio y carbono, materiales utilizados a menudo en el mundo aeroespacial, que garantizan resistencia y ligereza. Cada capa se coloca a mano por los trabajadores hasta alcanzar el número necesario para el tipo de casco que se va a fabricar.
Todo se hace tomando como base un molde de silicona, sobre el que se coloca la primera parte de las capas que se solidificarán en los congeladores especiales, y se procede a trabajar en dos semiesferas separadas, unidas después para tener el producto listo para pasar al siguiente departamento.
AquÃ, gracias a una maquinaria especÃfica, se afinan los detalles finales de los cascos en la versión de cuerpo-base y se perforan los orificios para las fijaciones de la visera, el Hans y los apéndices aerodinámicos donde sea necesario. Después viene la fase de pulido que deja el casco listo para adoptar su propia identidad.
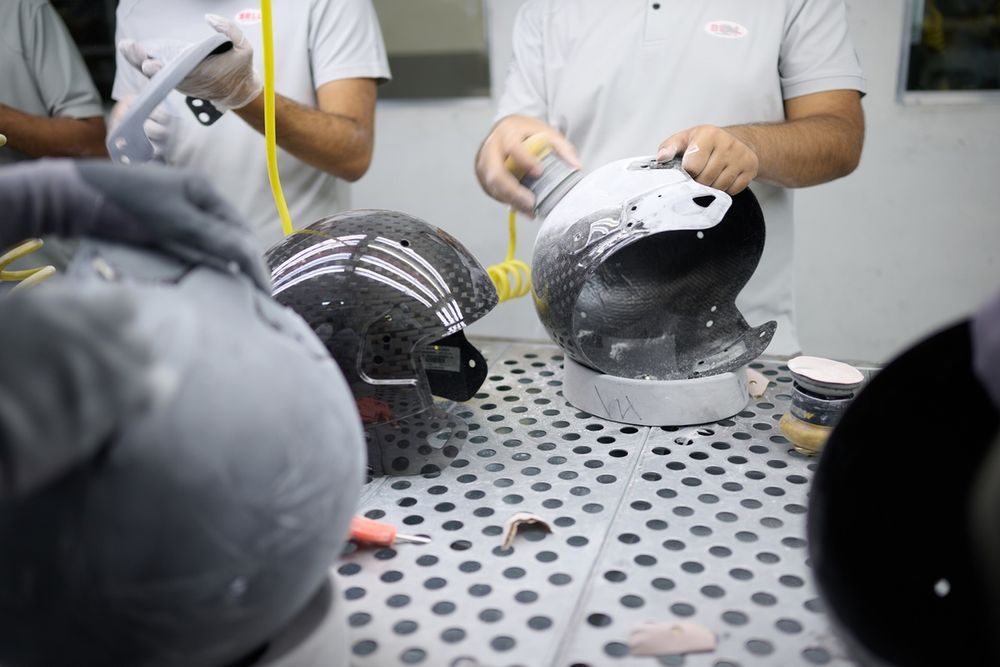
Departamento de paciencia
La visita continúa en las pequeñas salas dedicadas a la aplicación de logotipos, insignias y calcomanÃas de diversos tipos en función del producto que se vaya a crear. Es un departamento en el que hay muchas mujeres, y donde se requiere cuidado, atención y dedicación a los más mÃnimos detalles, resumidos en una sola palabra, paciencia.
Las calcas al agua se producen de manera interna y se colocan a mano con un tacto meticuloso, siguiendo el patrón impreso en las hojas que cada empleado tiene en su mesa frente a ella. Si alguna vez alguien trabajó con maquetas, sabrá muy bien lo difÃcil que es tratar con calcas grandes, pasándolas primero por la bandeja de agua y sacándolas después con pinzas donde se desee para su aplicación.
El mismo procedimiento se adopta también para los minicascos de coleccionista, que, además de una evidente base de plástico en lugar de carbono y demás, están decorados con exactamente los mismos detalles que los reales, siguiendo exactamente todas las instrucciones de la imagen de referencia. Una delicia fue poder ver un adelanto de los cascos que Carlos Sainz y Fernando Alonso utilizarán en el Gran Premio de Las Vegas, que, por supuesto, siguen siendo alto secreto y cuya filmación está prohibida.
Al lado está el taller de pintura, donde los trabajadores colorean los cascos con sus pistolas, y se necesitan de seis a doce meses de formación y entrenamiento para lograr la precisión y la perfección necesarias. A continuación, los cascos pintados y listos se colocan en los carros del pasillo principal para pasar al último “esfuerzo”.
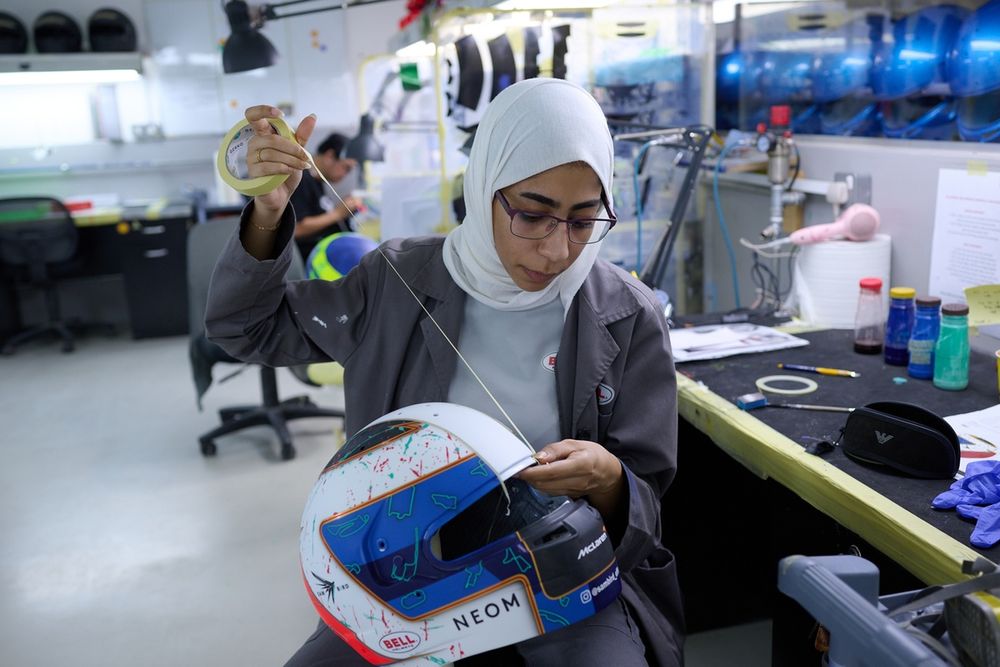
La… cosa de campeones
La gran final vuelve a estar reservada en su mayor parte a las mujeres, quienes se ocupan de tener precisión y perfección en el arte de confeccionar los componentes interiores de cada casco. Todos los puestos están rodeados de telas, tijeras, metros, material de costura y todo lo necesario para ajustar las distintas piezas, y no es poca cosa, hay que tener en cuenta no solo el tamaño de la cabeza, sino tambiénlos peinados.
El ejemplo puede ser el de Lewis Hamilton, que desde hace algún tiempo opta por el pelo largo con trenzas, lo que aumenta inevitablemente el volumen de su cabeza y obliga a modificar los refuerzos y forros del interior de su casco. Aquà también está el departamento para los minicascos de coleccionista, equipados con los mismos materiales de confección para una verdadera obra de arte de coleccionista hecha a mano por quienes estudian, crean y producen los auténticos cascos de pista, en definitiva, un dos en uno.
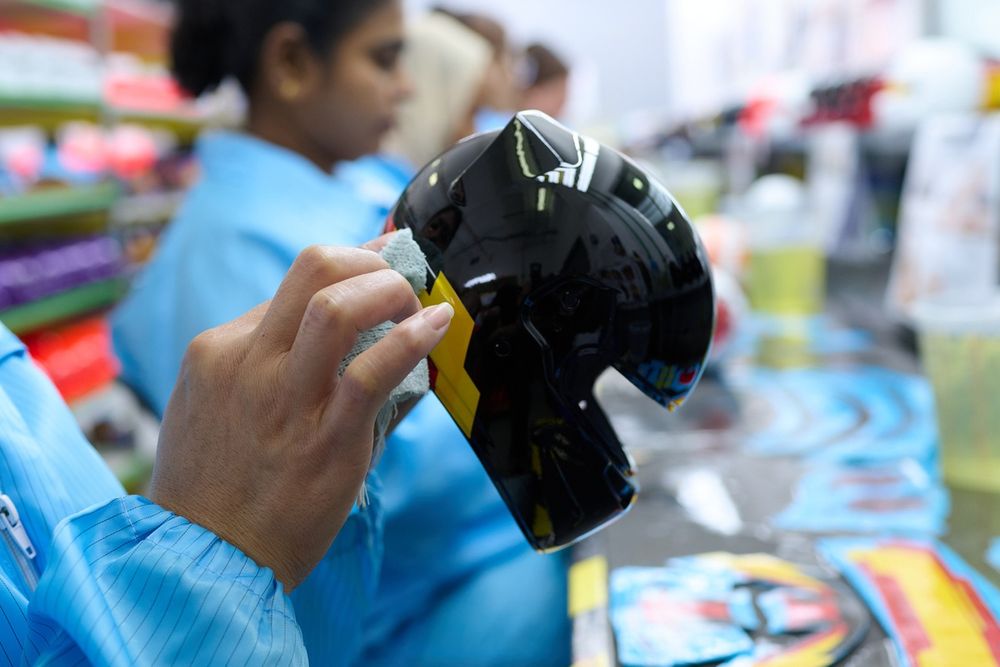
El arte de los números
Pasando a las cifras, cada año salen de aquà más de 40.000 cascos de competición y más de 70.000 minicascos para el mercado de modelos y coleccionistas, pero la empresa es capaz de aumentar los volúmenes respondiendo al crecimiento del mercado, más aún con la ampliación de la fábrica mediante la construcción de la segunda planta mencionada al principio.
En quince dÃas, los ingenieros y emplados de Bell son capaces de producir un casco partiendo de una hoja en blanco y llegando a la puesta en el mercado, o a la entrega directa al piloto que lo utiliza. En la Fórmula 1, actualmente 14 de 20 pilotos llevan cascos Bell, mientras que en el WEC, la media de los que llevan la marca es de unos 50, con más de 70 solo en las 24 Horas de Le Mans, pero la elección no suele ser solo a nivel personal, sino también a nivel de equipo, ya que Ferrari tiene un acuerdo para suministrar cascos a todos sus pilotos oficiales.
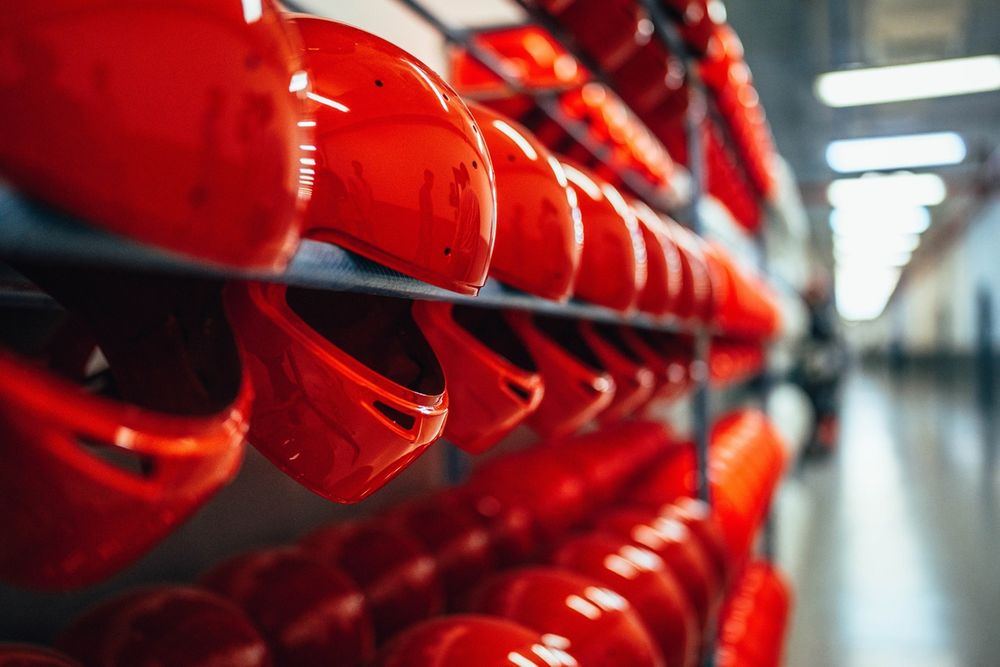
“Un aspecto que caracteriza a nuestra marca es que producimos internamente la gran mayorÃa de los componentes de un casco. Somos un fabricante, no solo un ensamblador, el proceso de producción está totalmente bajo nuestro control, hasta las pruebas finales de conformidad”, afirmó el director comercial de Racing Force y director de la planta de Bell en Bahrein, Aref Yazbek.
“Los minicascos Bell son una producción paralela, que comparte el mismo equipo de ingenierÃa y proceso de fabricación con los cascos de competición. Nuestros minicascos no son juguetes, sino verdaderas reproducciones a escala de un casco de carreras, utilizando las mismas materias primas y técnicas de fabricación”, continuó. “Es un negocio de rápido crecimiento y una gran herramienta de marketing, con la que también podemos acercarnos a un público de no profesionales, ávidos de un objeto de coleccionista que les vuelva a conectar con sus pilotos favoritos y su pasión”.
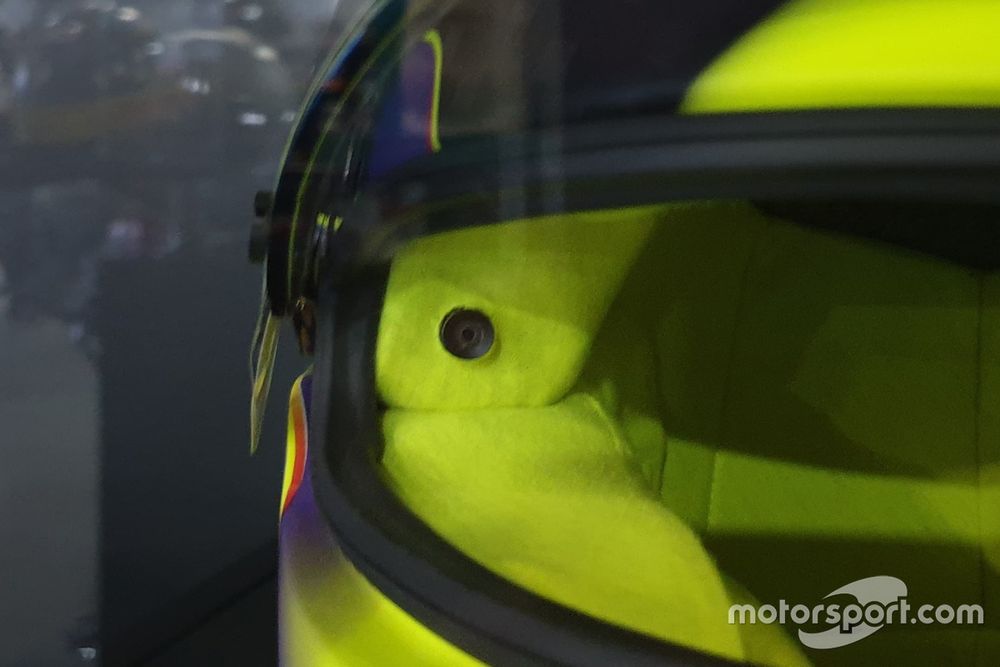
El ojo del casco
Hoy en dÃa, hasta los cascos tienen ojos. Es el ejemplo llevado a la pista hace unos años por la Fórmula E y la Fórmula 1, que integraron una pequeña cámara en el acolchado lateral interior para ofrecer imágenes lo más parecidas posible a lo que ve el piloto cuando conduce.
La ‘cámara del casco’ u ‘ojo del piloto’, como la rebautizaron las distintas categorÃas, es la cámara más pequeña del mundo para emitir en directo, pesa 1,43 gramos y tiene un diámetro de 9 milÃmetros. No está a la venta en el mercado, pero está vinculada a un servicio tecnológico que Racing Force Group presta a la Fórmula E, la primera en introducir esta joya en 2020, y a la Fórmula 1, y que también adoptó últimamente la NASCAR y los Supercars australianos.
También se establecieron contactos con Oakley para disponer de la misma tecnologÃa también en el esquÃ, la primera competición fuera de los circuitos, aprovechando no solo la mejora de la calidad del producto, sino también garantizando la seguridad porque la cámara no tiene ningún impacto ni efecto, al estar instalada en una posición en la que no se altera ningún parámetro de resistencia al impacto dentro del casco.
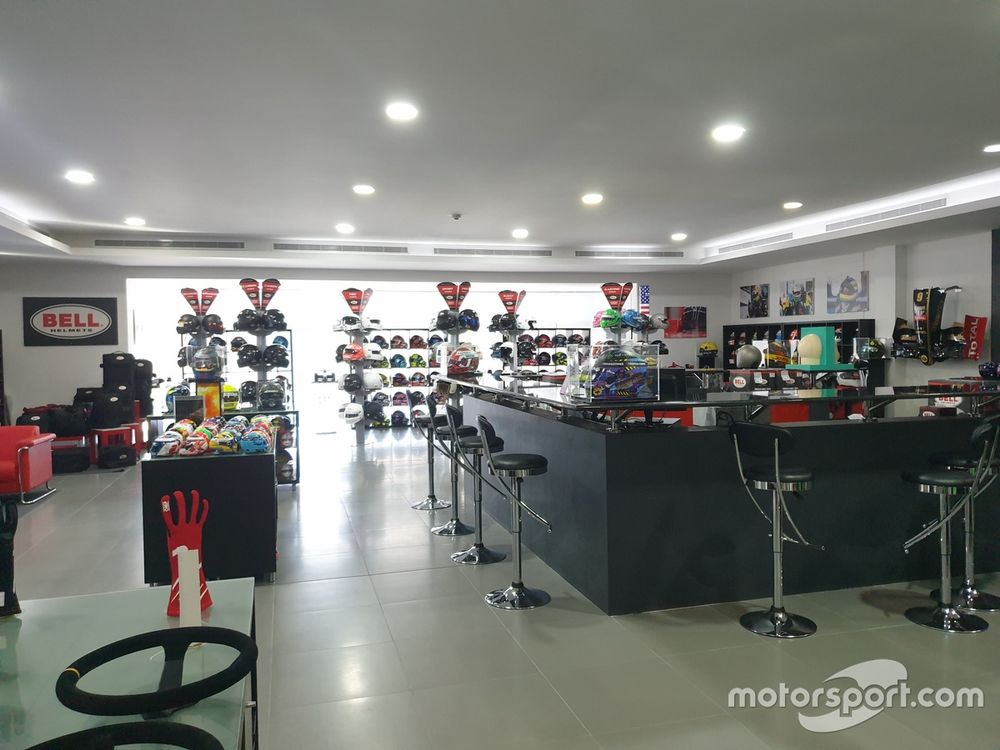
El casco Graal
El showroom abierto al público no es solo una sala de exposición de productos para elegir y comprar directamente para quien los necesite de inmediato, recordemos que a menos de un kilómetro está el circuito de carreras de Sakhir. Las estanterÃas de la mayorÃa de las paredes son una especie de museo de cascos de los distintos pilotos de ayer y de hoy, algunos con su ‘mini’ apoyado en el lateral, pudiendo asà admirar también la evolución a lo largo de los años y épocas del automovilismo mundial.
Sin embargo, está claro, que la pieza grande, pero grande de verdad, es la que está colocada sobre una base de cerca de un metro y medio de altura. Todo el mundo recordará lo que ocurrió en la salida del Gran Premio de Bahrein, celebrado el 29 de noviembre de 2020, cuando Romain Grosjean se estrelló contra las barreras a 67G, al salir de la tercera curva , quedando atrapado durante casi medio minuto entre las llamas de su Haas partido en dos.
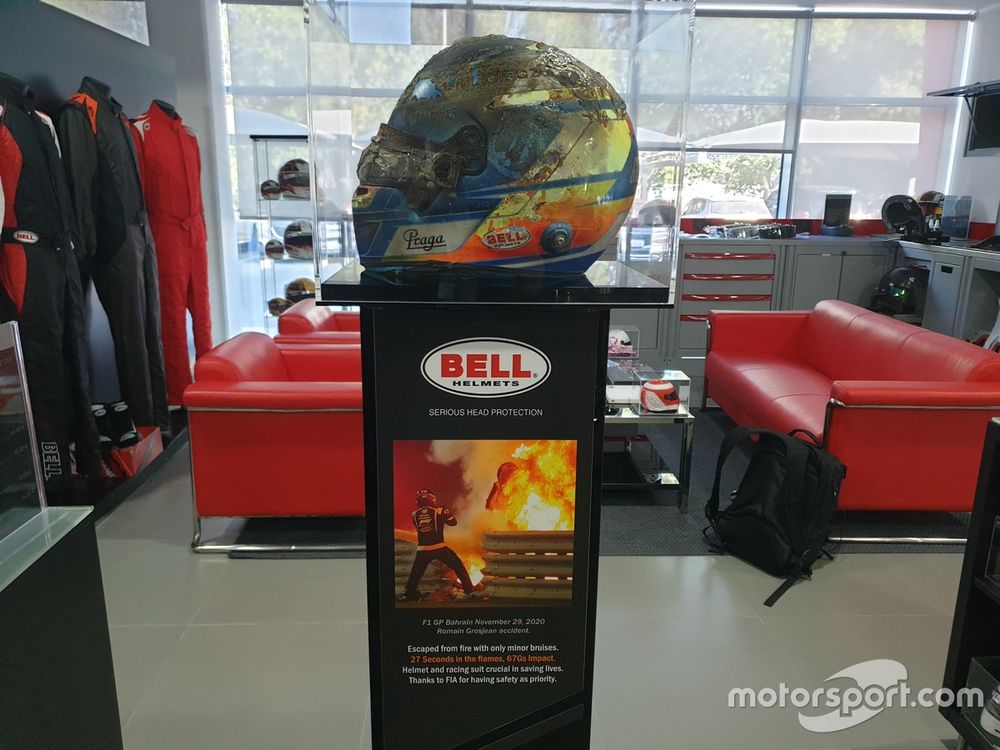
El piloto francés logró salvarse milagrosamente y su casco nunca ha salido de Bahrein, ahora expuesto en la sala de exposiciones de Racing Force Group no solo como una reliquia única, sino también como un sÃmbolo de la capacidad del producto que cumple con todas las normativas, incluidas las que exigen parar soportar las llamas, y con filtros de aire para garantizar una respiración lo más limpia posible en casos extremos como el de Romain Grosjean, que durante casi medio minuto se encontró en medio de unos humos tóxicos.
“Escapó de las llamas solo con quemaduras leves, 27 segundos en el fuego, 67G de impacto. El casco y el traje fueron cruciales para salvar vidas, gracias a la FIA por tener la seguridad como prioridad”.
Esta es la inscripción colocada bajo un casco que sigue en excelentes condiciones, con signos evidentes de quemaduras superficiales y la visera medio derretida, pero todavÃa con todo o casi todo en su forma original. Racing Force Group no permite que el casco del galo se utilice para ningún fin, sino que lo conserva como una verdadera reliquia, una especie de trofeo ganado sobre el terreno en una situación dramática que puso de relieve la calidad de la investigación tecnológica de vanguardia, motivo de orgullo para todas las partes implicadas.
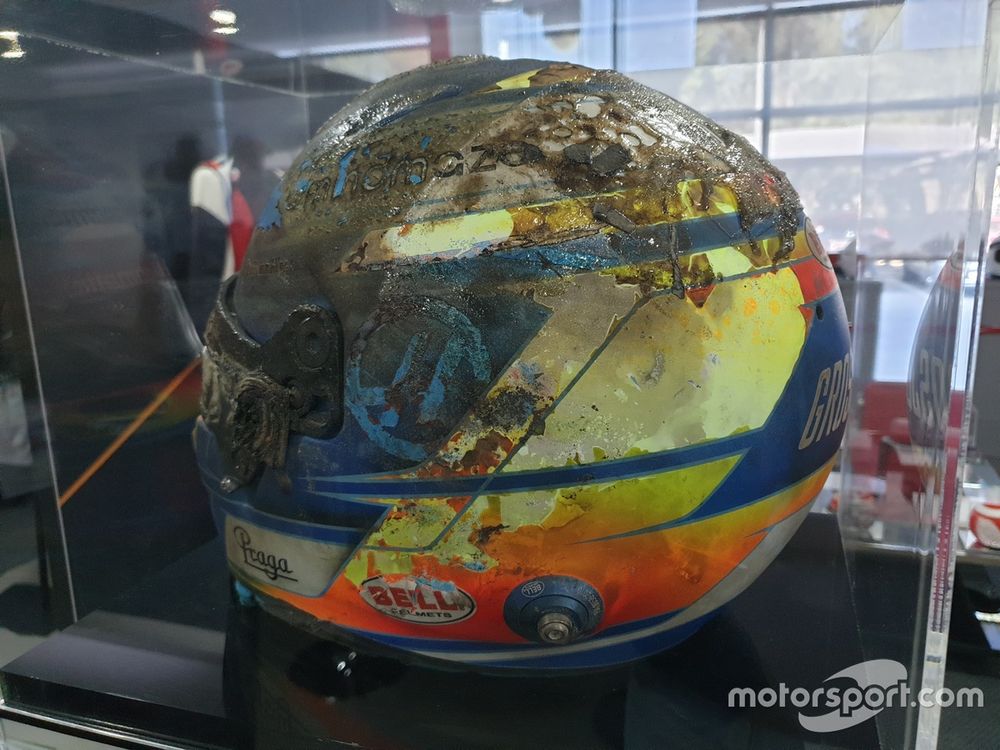
Aquà no solo hay de todo para los pilotos de todas las categorÃas, desde los karts hasta los coches de ruedas cubiertas, con cascos, guantes, monos, zapatos y todas y cada una de las piezas que pueden utilizarse en el equipamiento de carreras. Los entusiastas también tienen su propio departamento relacionado con los minicascos, donde es posible comprar recambios, con viseras, tornillos y todo lo que sea potencialmente frágil y que pueda recibir daños.
Otra joya de la calidad del producto a destacar, representada por el precio de venta, las minicajas rondan los 160 euros, con claras variaciones de costes en función de la tirada, el modelo y la particularidad del objeto, de una auténtica joya artesanal, construida directamente por las mismas personas que se ocupan de los originales.
Asà pues, qué se puede añadir, salvo que fue un privilegio experimentar y aprender tanto sobre tecnologÃa y seguridad en este único y auténtico Bell.
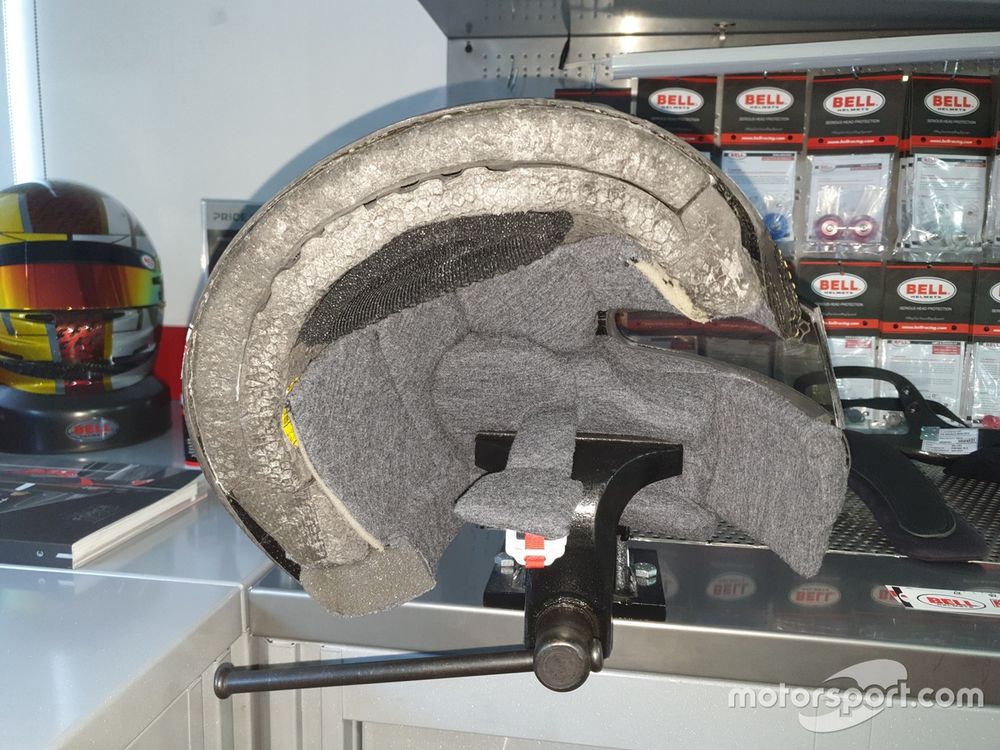
¿Quieres leer nuestras noticias antes que nadie y de manera gratuita? SÃguenos aquà en nuestro canal de Telegram y no te perderás nada. ¡Toda la información, al alcance de tu mano!